
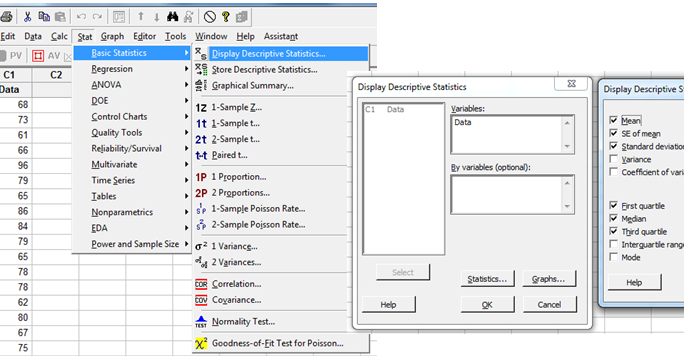
So what is a good şevel? In a world that operates on a level of 3.8, two short or long landings take place at a major airport per day. When we look at real world examples, the meaning of Sigma Levels becomes quite clear. Sometimes statistical terms can seem arbitrary and abstract. To compare process performance across an entire organization, the Sigma Levels of processes, One Sigma, Two Sigma, Three Sigma, Four Sigma, Six Sigma, etc. We use the metric, Defects per Million Opportunities, or DPMO, to calculate the Sigma Level for a product or process. Now, let’s look at Sigma Level: it is a high-level baseline metric to understand process capability to meet customer requirements. Sigma is a measure which uses the characteristic of past data to make judgments about how the process will perform in the future. Collecting data from a process’ performance will show the variation or Standard Deviation of the process’ performance. Standard Deviation is one of the absolute measures of dispersion or variation in data. Let us first understand what the word ‘Sigma’ means.
3 sigma vs 2 sigma how to#
In this article, we will go through this metric of Six Sigma by looking at its meaning and definition, its correlation between Defects per Million Opportunites ( DPMO), and how to calculate it by giving some examples.
3 sigma vs 2 sigma free#
This is the basis of all Six Sigma projects.Īttend our 100% Online & Self-Paced Free Six Sigma Training. There is one particular statistical term that is critical for Six Sigma and for understanding a process based on Six Sigma principles as briefly taught in free Six Sigma courses. Since we’re working with data, it is natural that we will work with statistics as you will learn in any reputable Six Sigma Green Belt training. In other words, although statistical tables indicate that 3.4 defects / million is achieved when 4.5 process standard deviations (Sigma) are between the mean and the closest specification limit, the target is raised to 6.0 standard deviations to accommodate adverse process shifts over time and still produce only 3.4 defects per million opportunities.The Six Sigma approach is a data-driven approach to problem-solving. * The table assumes a 1.5 sigma shift because processes tend to exhibit instability of that magnitude over time.

The other side of the process distribution, which may have a tail beyond the farther specification, is ignored by the Cpk calculation. Note: the conversion of Sigma Level to Cpk is only an approximation because Cpk is based only upon the specification limit closest to the process mean. The 1.5 sigma shift may or may not be an accurate estimate of the actual long-term instability of your process.
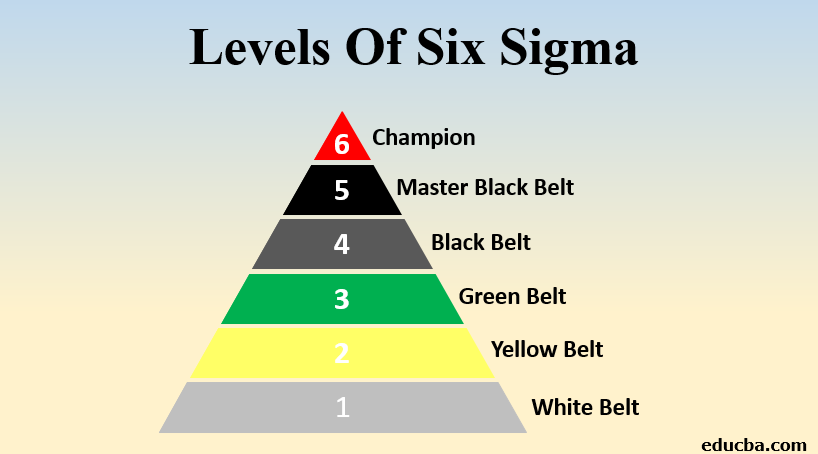
In essence, the 1.5 sigma shift indicates that if you intend to have 3 DPMO over the long term, the process must be more capable than the 4.5 sigma (Cpk) indicated by a normal curve in order to accommodate instability or process shifts that occur over time. By convention established at Motorola, where the Six Sigma program originated, the Sigma level is adjusted by 1.5 sigma to recognize the tendency of processes to shift over the long term. The following table lists Defects Per Million Opportunities with the corresponding Sigma Level.Īlso shown is a direct conversion to a Cpk level based on the area under a Normal Curve.
